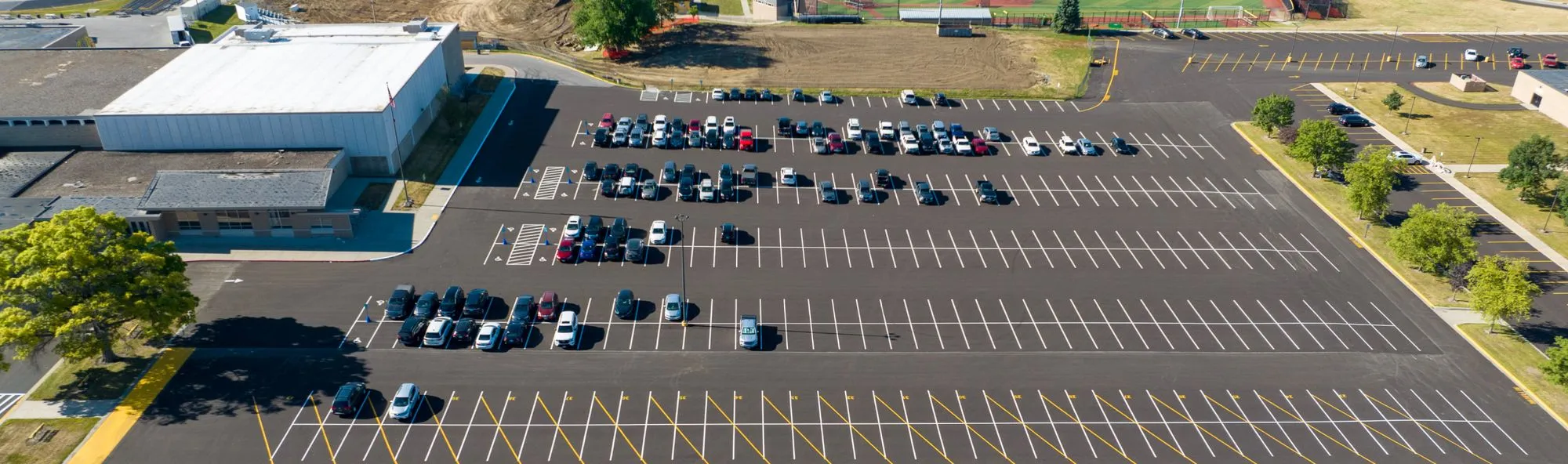
Paving the way.
We use recycled materials to create a more durable asphalt that lasts longer. Our NewRoad® technology is based on highly engineered recycled industrial polymers and is used in DOT, county and city roads, and in commercial parking lots and driveways.
How it Works
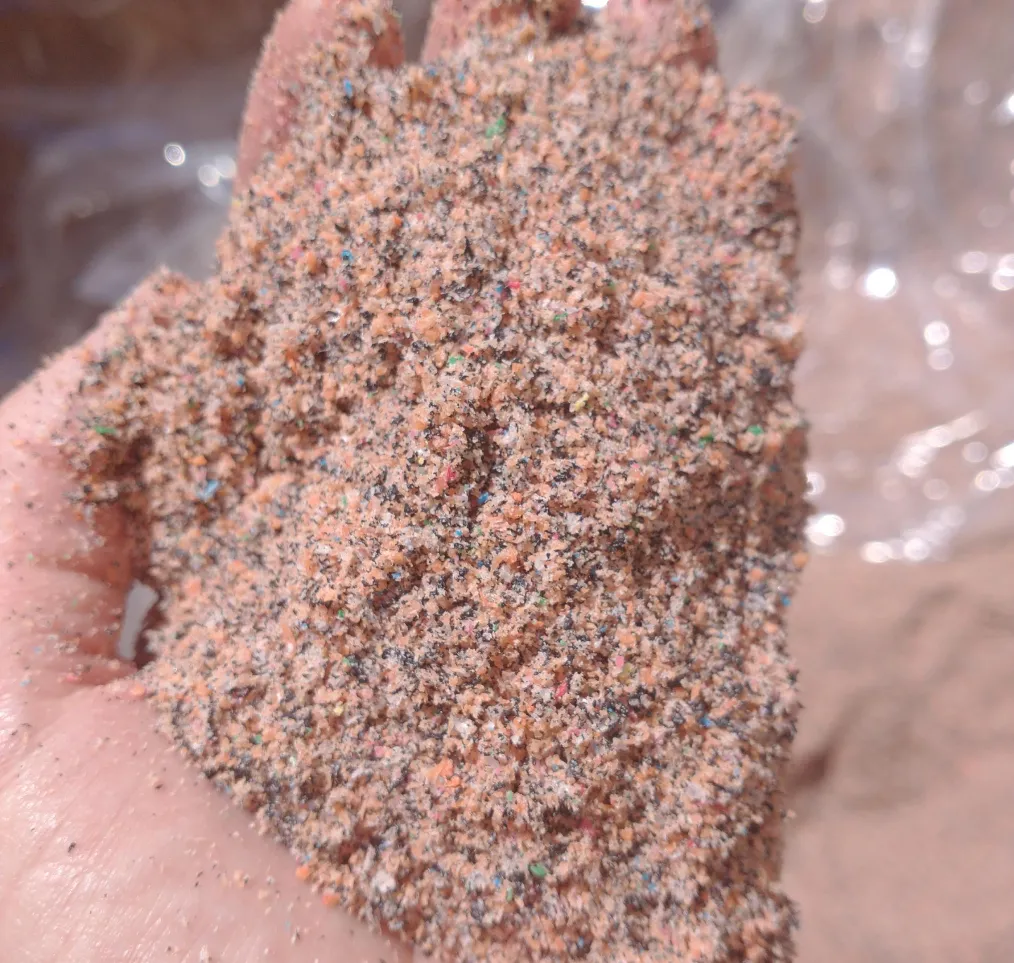
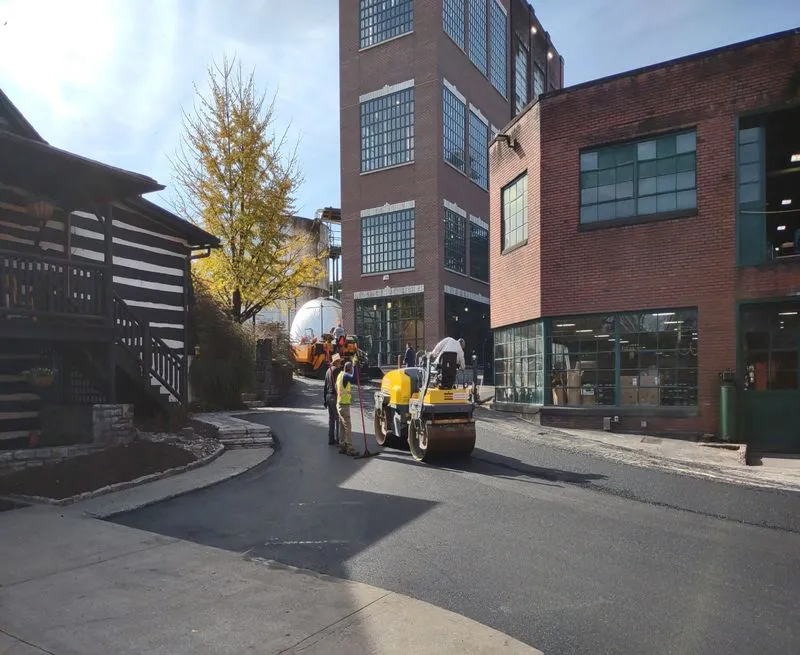
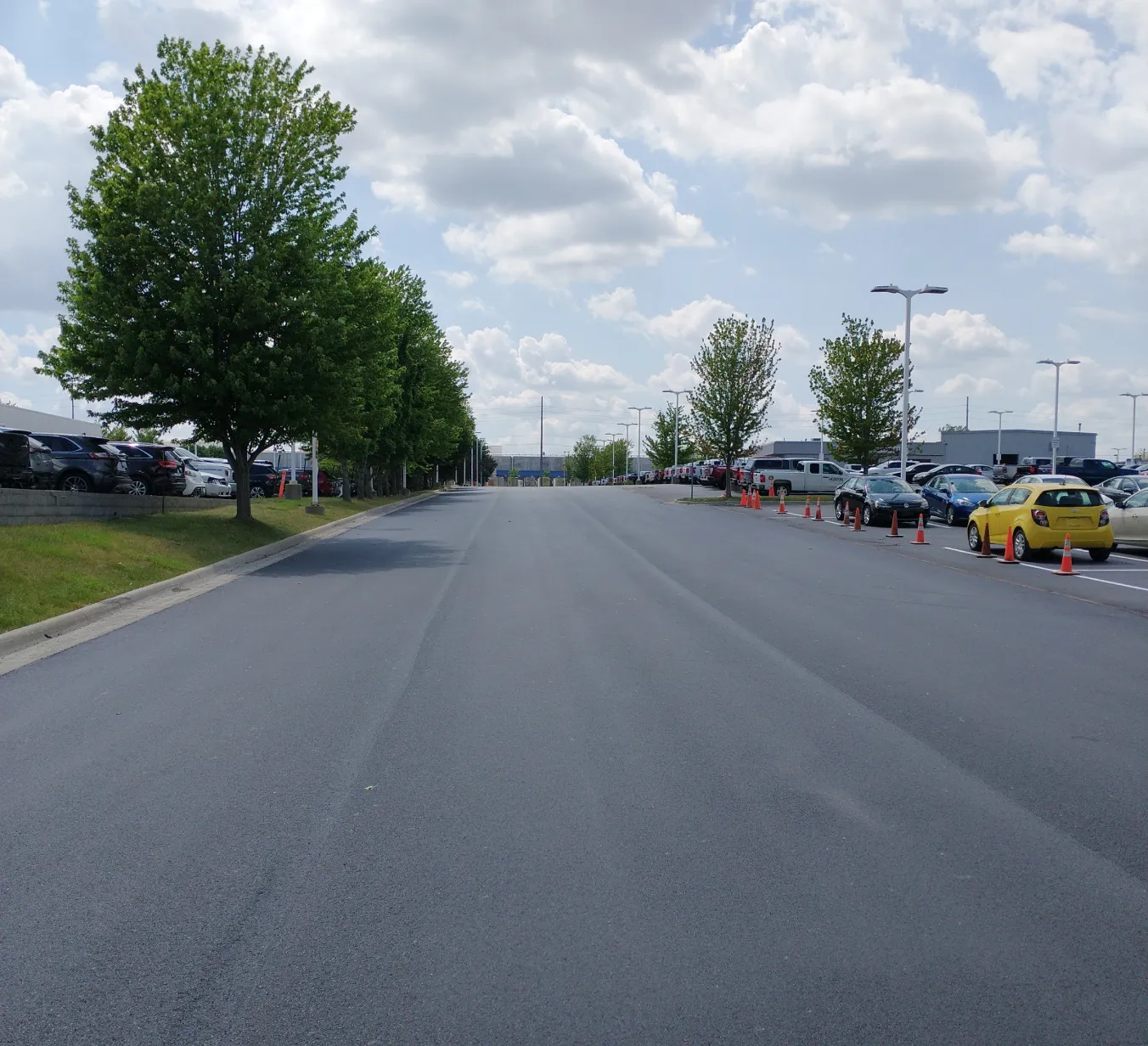
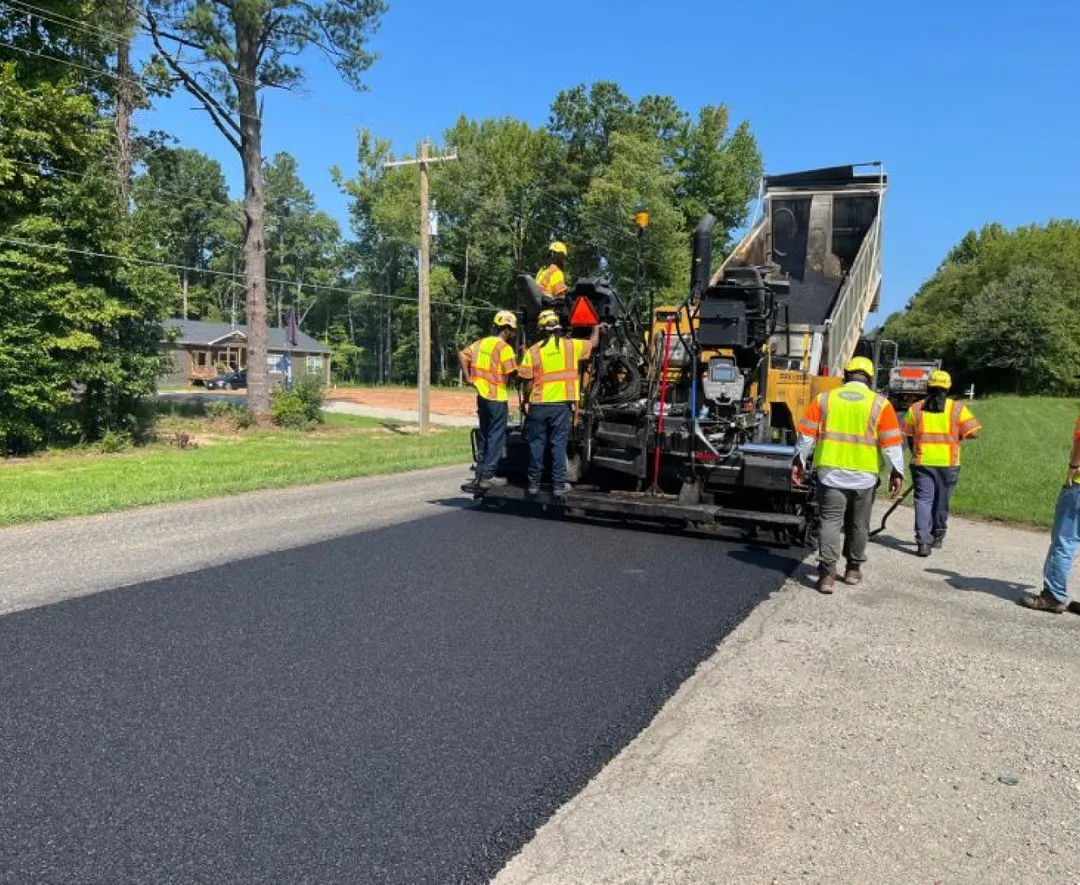
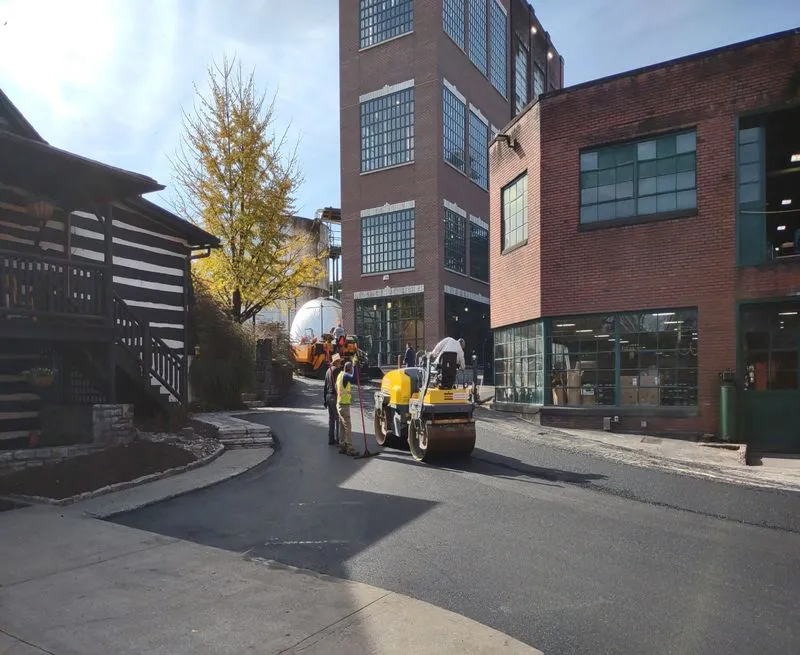
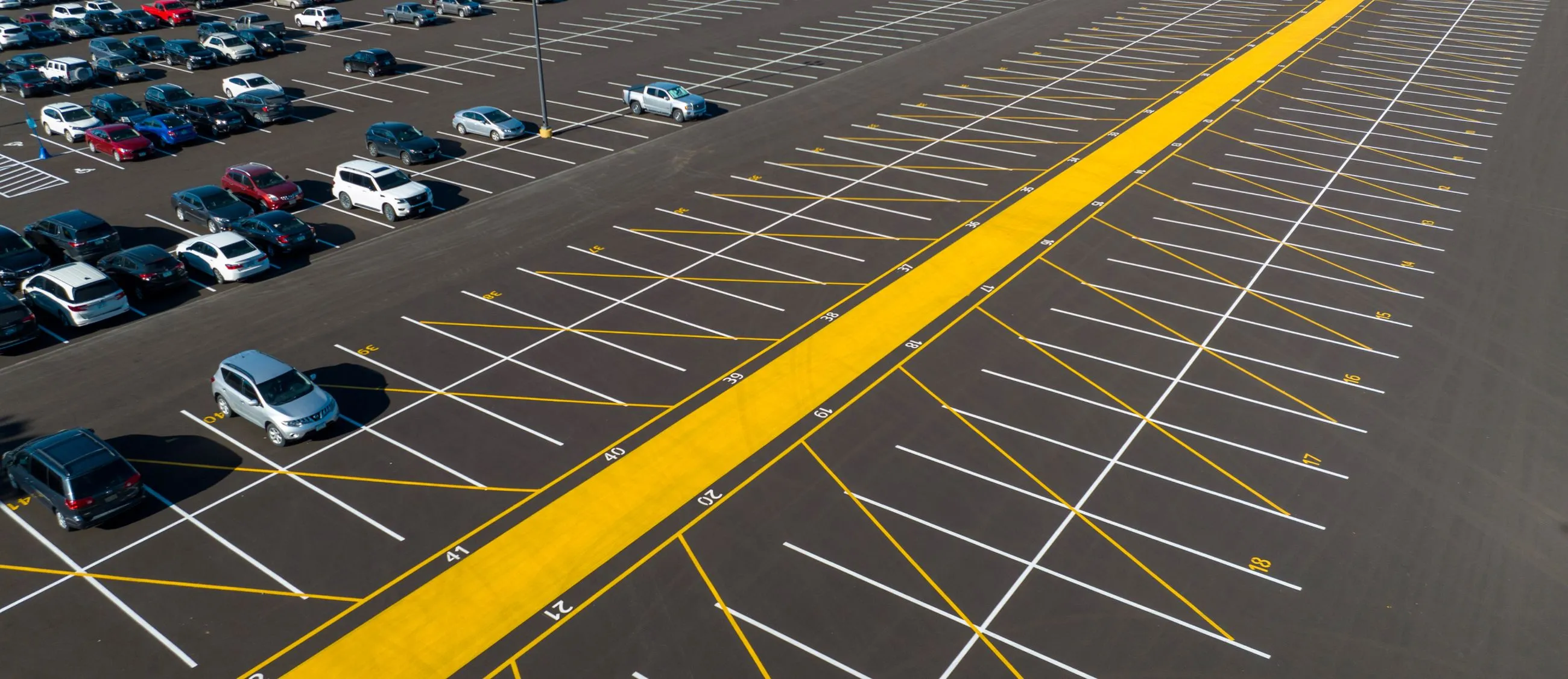
Application FAQ’s
NewRoad® is added to the asphalt mix with a dry process introduced on the RAP belt / RAP collar by a metering system. Mixing temperature usually remains the same, around 250°F (120°C).
NewRoad® is measured pound per ton, so dosage is generally very small.
We recommend 4lbs per ton of asphalt mix for maximum strength and durability.
No changes to volumetrics (air voids, Gmm, etc.)
Over 7 years in the field with no failures!
Most asphalt plants have the needed machinery, but NewRoad® is always happy to provide our own auger on-site to meter the product onto the RAP belt.
Reach out for a quote or an introduction call!
info@newroad.com
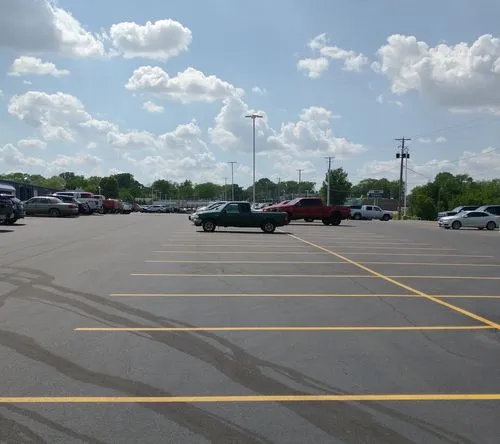
Resilient Roads.
Cost Effective Projects. Longer-Lasting Lots.
Case Studies
Just the facts, in black and white.
Just the facts, in black and white.
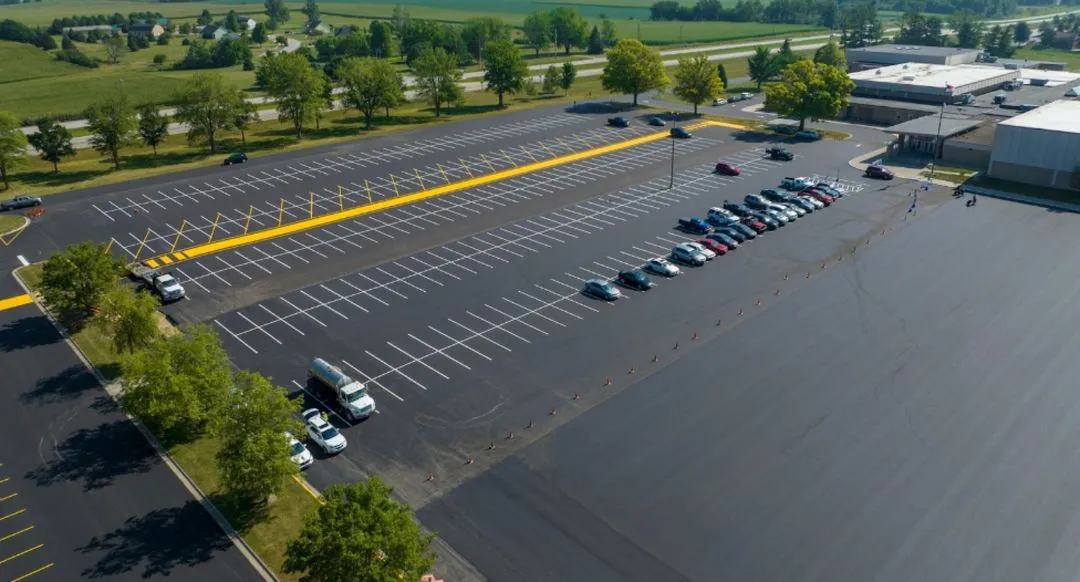
The CT Index, also known as IDEAL-CT, is a common cracking test that many state transportation agencies use to estimate the fatigue performance of asphalt mixes. The test is performed at room temperature (77°F) in the Lottman test equipment. The test evaluates the strength of an asphalt mix and how quickly the specimen cracks after the maximum strength, making it a good indicator of sufficient asphalt binder for a given mix. The test provides relative rankings of similar types of asphalt mixes.
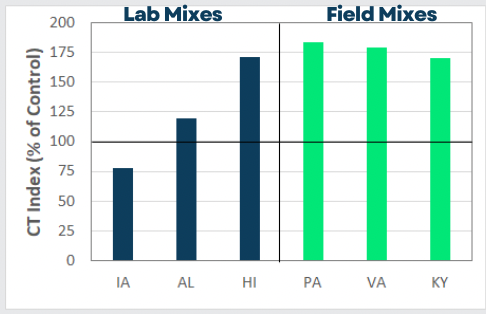
Field Mixes: Consistent improvement - NewRoad® acts like additional binder when well-blended in the field, which improves the rate of cracking and results in a higher CT Index.
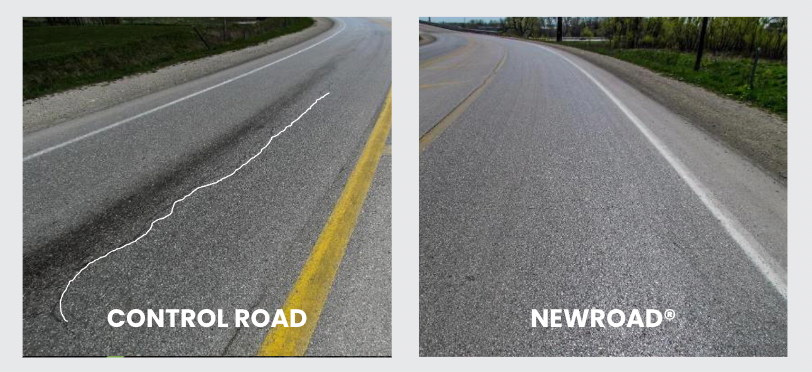
The Hamburg Wheel Tracking Test (HWTT) per AASHTO T 324 is widely used by asphalt researchers and pavement engineers to evaluate the rutting resistance and moisture susceptibility of asphalt mixtures. A loaded steel wheel tracks over the samples in a heated water bath, while the deformation is observed vs. the number of loading passes. The images below show 20,000 passes with differing amounts of NewRoad® additive.

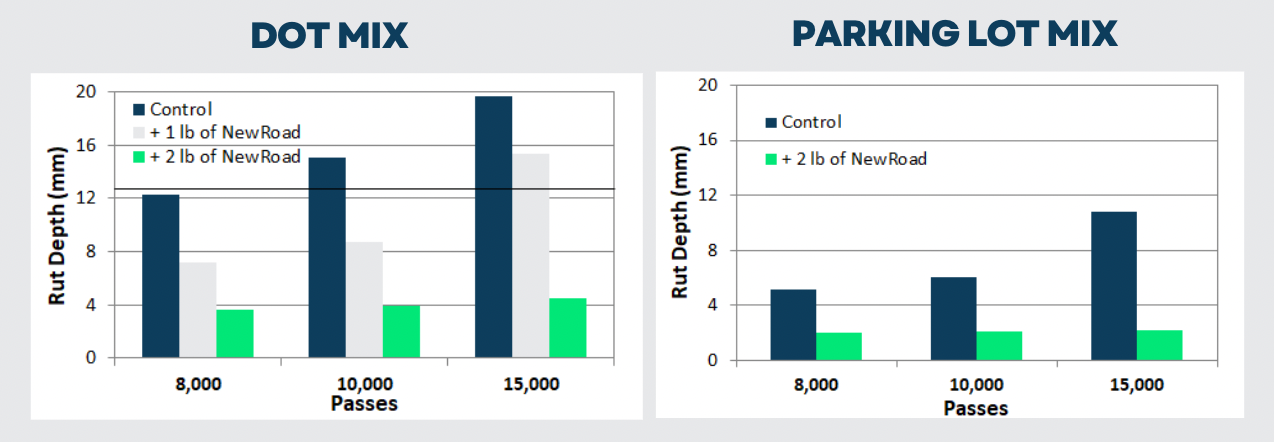
Adding 1 lb of NewRoad® per ton of mixture greatly reduces the rut depth, which improves the safety of the pavement, and increases the failure point to 13,000 passes (45% increase in pavement life).
Adding 2 lbs per ton of mixture creates a stable, durable mix that keeps water out of the pavement.inside of a div block.
A concern of using plastics in pavement is the potential generation of microplastic particles from the degradation of the original plastic component into tiny particles due to exposure to environmental conditions such as ultraviolet light, weathering, and abrasion. The following results show that the NewRoad® additive does not increase the release of microplastics, but instead improves the internal mixture bonding to contain the microplastics within the asphalt mix.
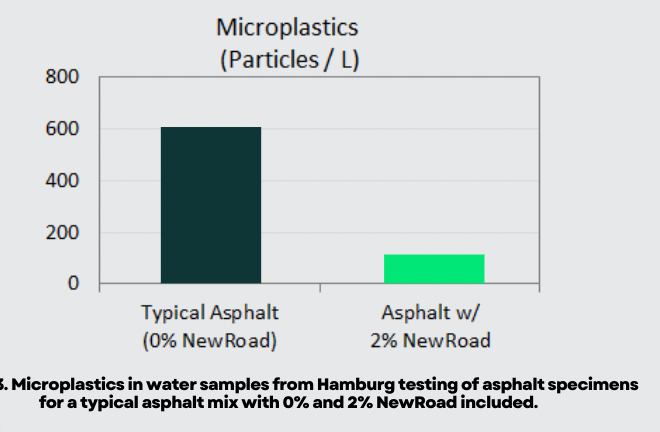
Established in 1986 as a partnership between Auburn University and the National Asphalt Pavement Association (NAPA) Research and Education Foundation to provide practical research and development to meet the needs of maintaining America's highway infrastructure. NCAT's mission is to provide innovative, relevant and implementable research, technology development and education that advances safe, durable and sustainable asphalt pavements. In 2021, NewRoad® provided samples to NCAT to perform independent third-party performance research.
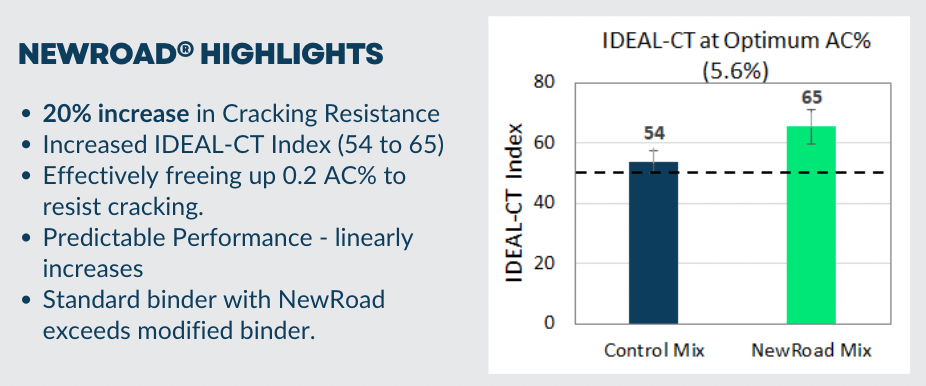
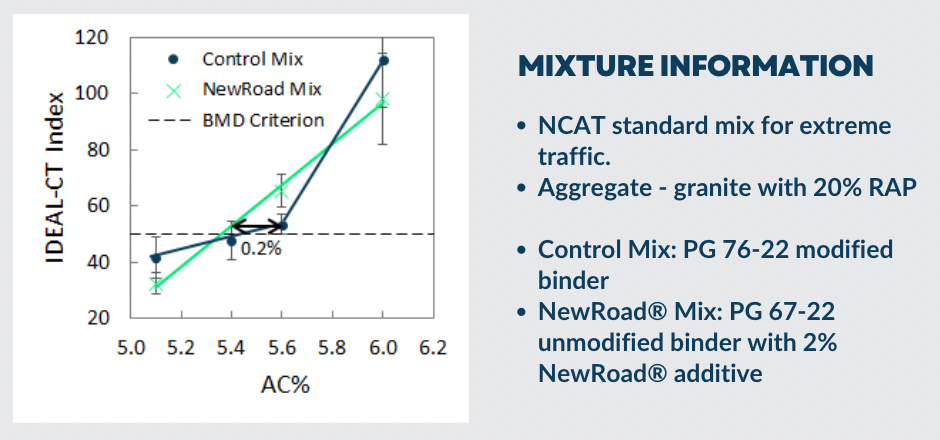
The fuel resistance testing was performed by following the procedure listed in the FAA P404 standard for fuel-resistant asphalt mixes. A 9.5 mm mixture with a 5.8% asphalt content was tested. The mixture was compacted using 50 Marshall blows to fabricate specimens with 5.0% air voids. The specimens were placed in kerosene for 24 hours to determine the amount of asphalt that was dissolved by the kerosene. The specimens were weighed before and after 24 hours of soaking in kerosene to determine the % Loss (Weight Loss / Total Initial Weight * 100).
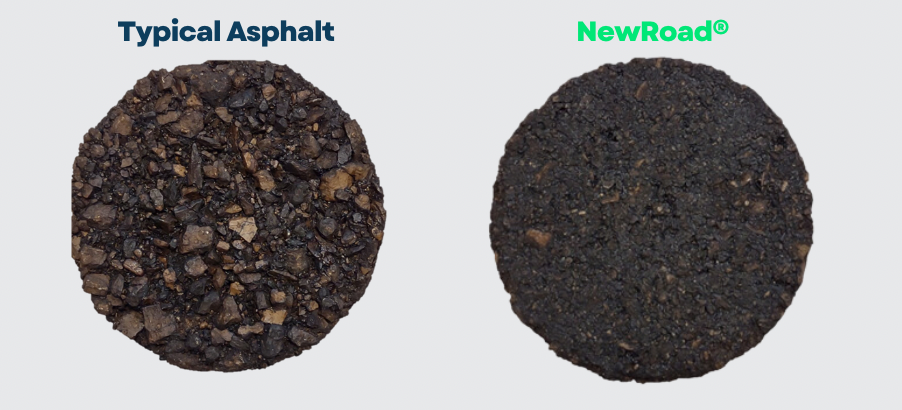
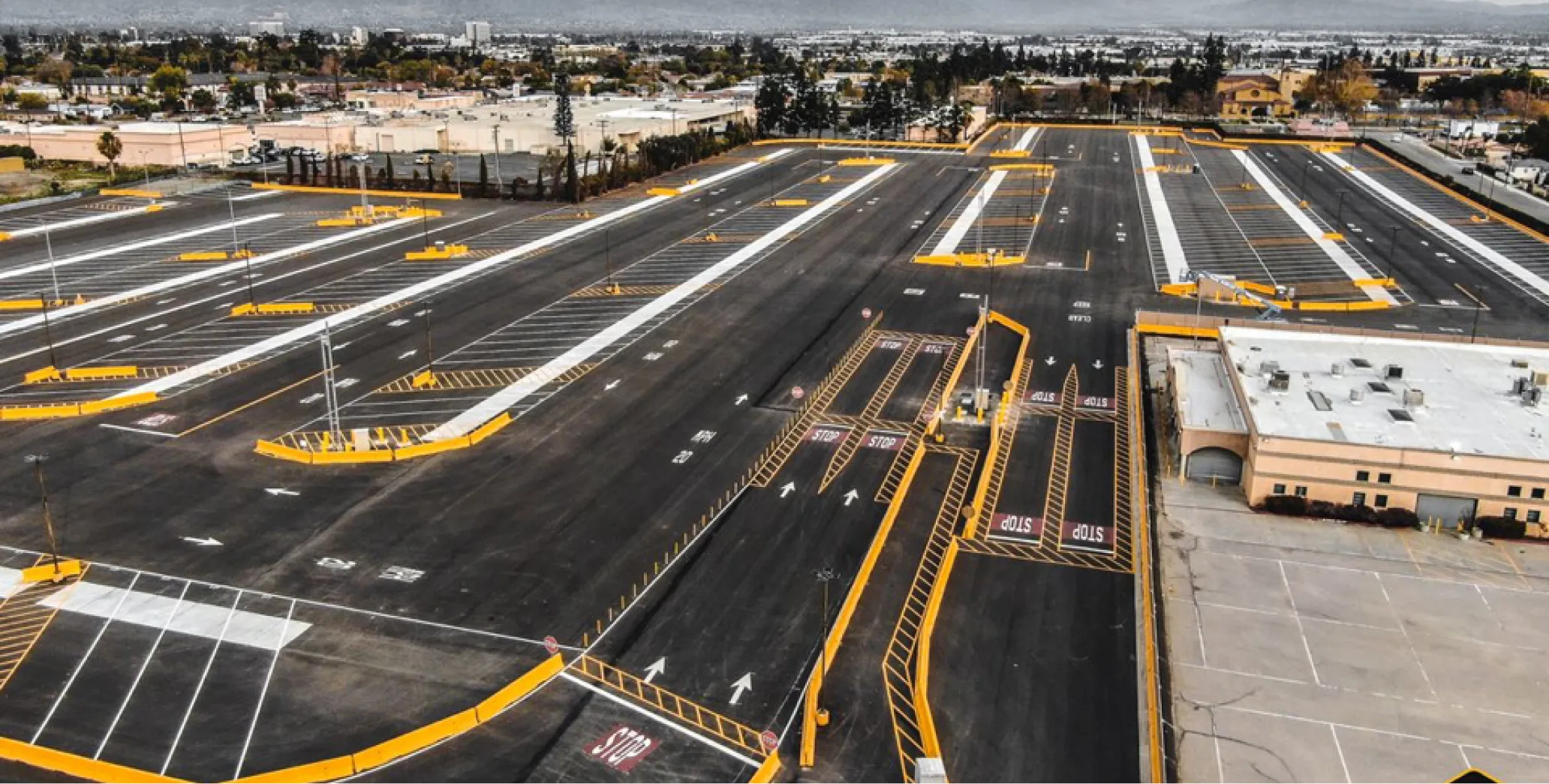
Ready to work together?
Reach out to get information in less than 24 hours.
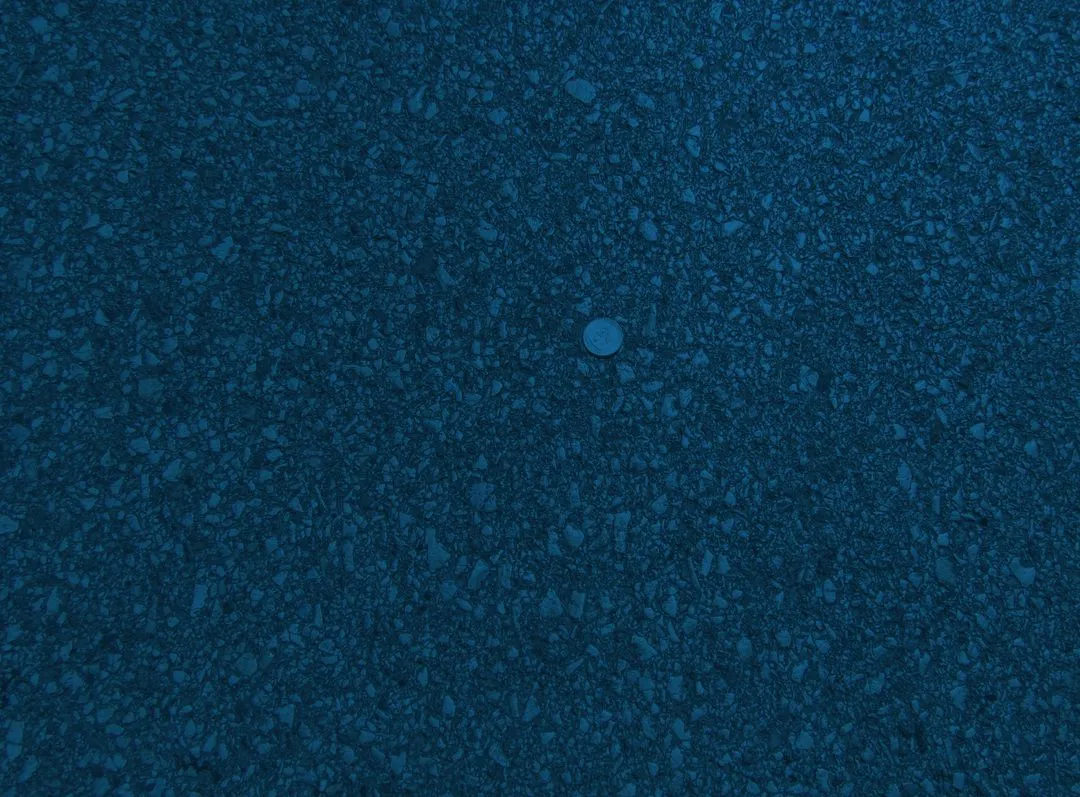
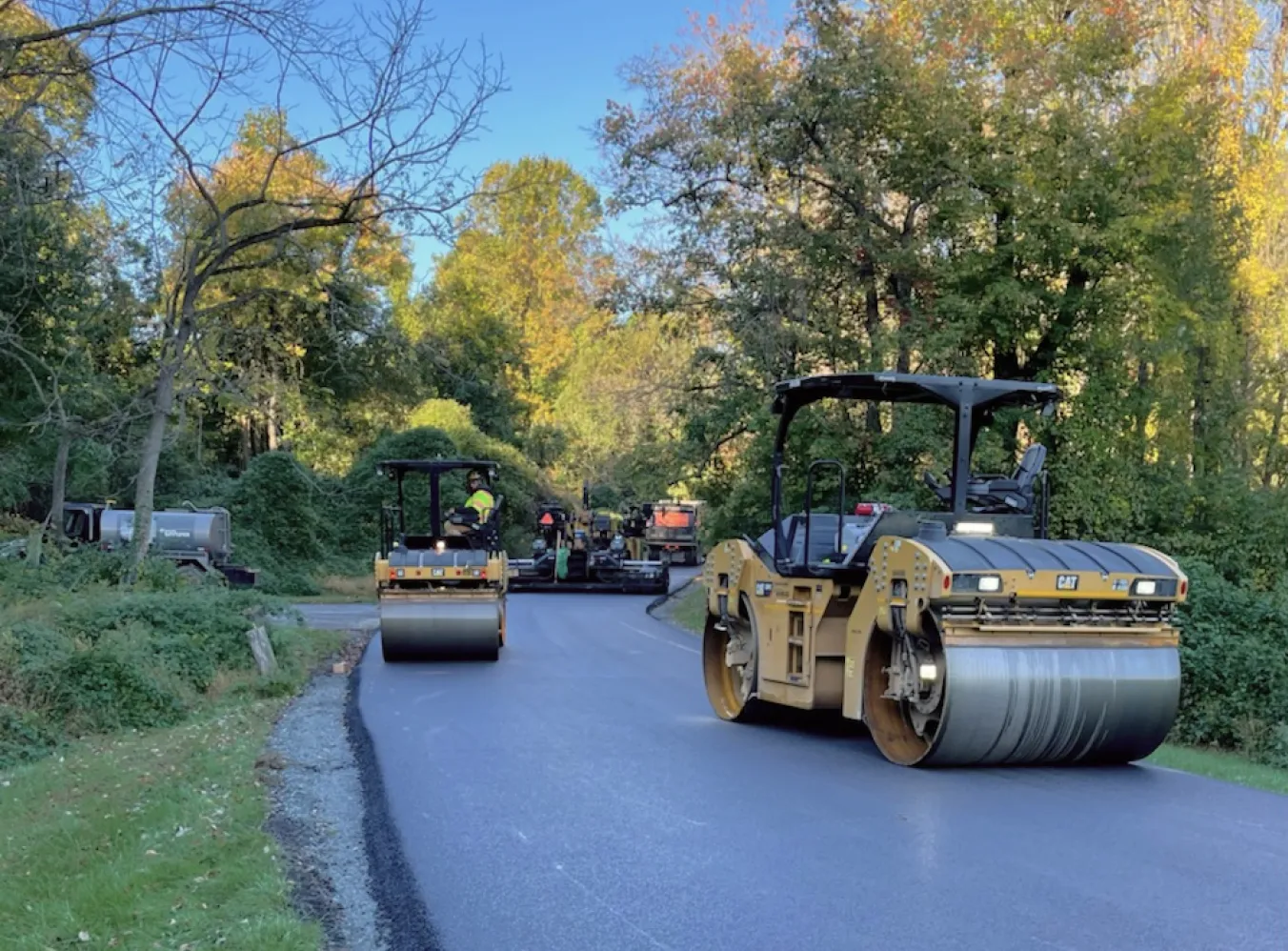